DC Controllers
DC Motor Controllers & Drivers
A DC motor controller is an electronic device that regulates the speed and direction of a DC (direct current) motor. It serves as an intermediary between the power source and the motor, providing a controlled flow of electrical energy to achieve the desired motor performance. These controllers are crucial in various applications where precise motor control is essential, such as robotics, automation, electric vehicles, and industrial machinery.
The primary functions of a DC motor controller include:
- Speed Control: DC motor controllers modulate the voltage or current supplied to the motor, thereby controlling its speed. This is often achieved through methods like Pulse Width Modulation (PWM), where the average voltage determines the motor speed.
- Direction Control: DC motor controllers allow for the reversal of the motor's direction by changing the polarity of the supplied voltage or current. This capability is vital for applications requiring bidirectional movement.
- Efficiency Optimization: Advanced DC motor controllers may incorporate features like closed-loop feedback mechanisms to optimize the motor's efficiency. These mechanisms continuously monitor the motor's performance and adjust the control signals accordingly.
- Protection Mechanisms: Many controllers include safety features such as overcurrent protection and overtemperature protection to prevent damage to the motor and the controller itself.
- Specialized Control Features: Depending on the type and complexity, DC motor controllers can have additional features, such as regenerative braking (recovering energy during braking), integration with IoT (Internet of Things) for remote control, and compatibility with programmable logic controllers (PLCs) for industrial automation.
Price of DC Motor Drivers
The cost of DC motor controllers can differ depending on factors like features, power capacity, and brand. When making a purchase decision, carefully assess your project requirements and budget constraints. It's important to note that prices may change due to market trends and technological advancements. Seek the best value that aligns with your specific needs, ensuring a balanced investment without unnecessary overspending.
Types of DC Motor Controllers
DC motor controllers come in various types, each designed to meet specific requirements and applications. Here are some common types of DC motor controllers:
- Basic On/Off Switch: Simplest form of control, manually turning the motor on and off. Limited in terms of speed and direction control, suitable for basic applications.
- PWM (Pulse Width Modulation) Controllers: Modulates the width of the electrical pulses sent to the motor, controlling the average voltage and, consequently, the motor speed. Provides precise speed control and is energy-efficient.
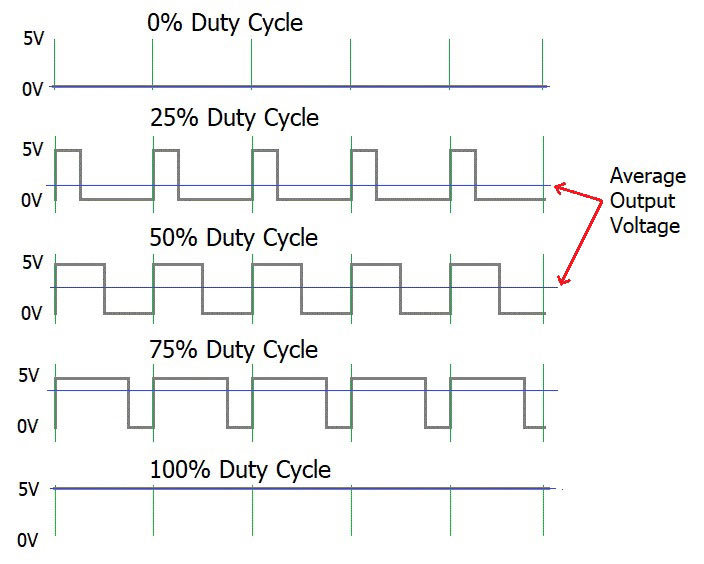
- H-Bridge Controllers: Utilizes an H-bridge circuit to control both the speed and direction of the motor. Commonly used in robotics and applications where bidirectional control is essential.
- Closed-Loop Feedback Controllers: Incorporates feedback mechanisms to continuously monitor and adjust the motor's speed for precise control. Offers enhanced stability and accuracy in maintaining the desired speed.
- Regenerative Braking Controllers: Captures and reuses energy generated during braking, improving overall energy efficiency. Common in electric vehicles and applications with frequent starts and stops.
- Brushless DC Motor Controllers: Specifically designed for brushless DC motors, providing control for applications requiring higher efficiency and reliability.
- Motor Drivers with Current Sensing: Monitors the current flowing through the motor, adjusting power to prevent overheating and protect the motor from damage. Common in applications where current fluctuations are a concern.
- High-Power Industrial Controllers: Engineered to handle heavy-duty applications with high power loads. Typically used in industrial settings where robust performance is essential.
Choosing the right type of DC motor controller depends on the specific requirements of your application, including speed precision, direction control, energy efficiency, and integration capabilities.
Top 10 Popular DC Motor Controller Models
- L298N Dual H-Bridge Motor Controller: A popular and versatile choice for small to medium-sized projects, providing bidirectional control.
- Motor Driver BTS7960B: Known for its high current capacity, suitable for applications requiring robust motor control.
- Pololu Jrk G2 USB Motor Controller: Ideal for users seeking advanced features like feedback control and USB connectivity for configuration.
- Sabertooth Dual 32A Motor Driver: Offers robust performance with dual channels, suitable for driving heavy-duty motors.
- Cytron 13A, 5-30V DC Motor Controller: Known for its compact size and high current handling, suitable for a wide range of applications.
- Roboclaw 2x7A Motor Controller: Featuring dual channels and versatile control options, it's favored for its reliability in robotic applications.
- MC33926 Dual Motor Driver Carrier: Known for its robust design and current sensing capabilities, suitable for automotive applications.
- DRV8833 Dual Motor Driver Carrier: A compact and cost-effective choice for simple motor control tasks, popular among hobbyists.
- L9110S Dual Motor Driver: Compact and cost-effective, the L9110S is suitable for smaller projects requiring bidirectional motor control.
- MX1508 Dual Motor Driver: Known for its ease of use and reliability, the MX1508 is favored for applications with moderate power requirements.
- L293D Quadruple Half-H Driver: A classic choice for robotics and hobbyist projects, the L293D provides versatile motor control capabilities.
- TB6612FNG Dual Motor Driver: With built-in protection features, the TB6612FNG is ideal for projects requiring precise and reliable motor control.
- DRV8830 Single Brushed DC Motor Driver: Compact and efficient, the DRV8830 is suitable for single-motor applications with tight space constraints.
What is a DC Motor Driver used for?
DC motor controllers serve a crucial role in various applications by regulating the speed and direction of DC (direct current) motors. Their versatility makes them essential in a wide range of industries and projects. Here are some common uses of DC motor controllers:
- Robotics: DC motor controllers are widely used in robotics to control the movement of robotic arms, wheels, and other components. They enable precise speed and direction control, contributing to the agility and functionality of robots.
- Automation Systems: In industrial automation, DC motor controllers are employed to control conveyor belts, assembly line components, and other machinery. The ability to adjust speed and direction ensures efficient and synchronized operation.
- Electric Vehicles: DC motor controllers play a crucial role in electric vehicles, controlling the speed and direction of electric motors used in propulsion systems. They contribute to the overall efficiency and performance of electric cars and bikes.
- Consumer Electronics: Various household appliances, such as fans, mixers, and power tools, use DC motors with controllers for precise speed and operation control. This enhances user experience and safety.
- HVAC Systems: Heating, ventilation, and air conditioning (HVAC) systems utilize DC motor controllers to regulate the speed of fans and blowers. This allows for efficient temperature control and energy conservation.
- Medical Devices: DC motor controllers are found in medical equipment such as infusion pumps, ventilators, and robotic surgical devices. They contribute to the precise and controlled movement of components in these devices.
- Aerospace Applications: In aircraft and aerospace systems, DC motor controllers are used in various applications, including controlling actuators, adjusting control surfaces, and managing auxiliary systems.
- Renewable Energy Systems: DC motor controllers are employed in renewable energy systems, such as solar tracking systems. They adjust the orientation of solar panels to maximize sunlight exposure and energy generation.
- Gaming and Hobbyist Projects: Enthusiasts and hobbyists use DC motor controllers in projects like remote-controlled cars, drones, and model trains. These controllers provide precise control over the motors, enhancing the overall functionality of the projects.
- Industrial Machinery: DC motor controllers play a vital role in various industrial machines, including conveyors, pumps, and manufacturing equipment. They contribute to efficient and controlled operation in diverse industrial settings.
In essence, DC motor controllers are used wherever precise control of motor speed and direction is required. Their adaptability and versatility make them indispensable in a wide array of applications across different industries and projects.
How does a DC Motor Controller work?
A DC motor controller functions by regulating the voltage and current supplied to a DC motor. Through voltage adjustments, it controls motor speed, and by managing current flow, it influences torque. Pulse Width Modulation (PWM) is often employed, rapidly switching the voltage on and off to adjust motor speed. For bidirectional control, an H-Bridge circuit facilitates forward and reverse rotation. Some controllers utilize feedback systems like encoders for precise speed and position control. Essentially, the controller acts as a mediator between the power source and the motor, ensuring optimal performance and allowing users to finely tune speed, direction, and overall operation
Can I use any DC Motor Driver with Arduino?
In general, you can use various DC motor controllers with an Arduino or any type of microcontroller. DC motor controllers come in different types and configurations, and their compatibility with Arduino depends on several factors. Here are some considerations:
- Voltage Compatibility: Ensure that the voltage requirements of the DC motor controller match the voltage supplied by your Arduino. Most Arduino boards operate at 5V, and there are also variants that operate at 3.3V. Check the voltage ratings of both the Arduino and the DC motor controller to ensure compatibility.
- Current Requirements: Check the current requirements of your DC motor and ensure that the DC motor controller can handle the required current. If the current demands of the motor exceed the capacity of the controller, you might need an external power supply for the motor.
- Control Interface: Different DC motor controllers use various control interfaces, such as PWM (Pulse Width Modulation), analog voltage, or serial communication. Ensure that the control method of the DC motor controller aligns with the capabilities of the Arduino. Many DC motor controllers accept PWM signals for speed control.
- Number of Motors: Consider the number of DC motors you plan to control with the Arduino. Some motor controllers are designed for single motors, while others can handle multiple motors. Ensure that the controller has the necessary channels for your project.
- Library and Code: Some DC motor controllers may come with specific libraries or require specific code for proper operation. Check the documentation provided with the motor controller and ensure that you have the necessary libraries installed in your Arduino IDE.
- Power Supply: If your DC motor requires a higher voltage than what the Arduino can provide, you may need an external power supply for the motor controller. Ensure that the power supply meets the requirements of both the controller and the motor.
What is PWM in DC motor controllers?
PWM, or Pulse Width Modulation, is a fundamental technique employed by DC motor controllers to regulate the speed of a motor. Through rapid switching of the voltage on and off, the controller effectively controls the average power delivered to the motor, influencing its speed. PWM allows for precise speed adjustments, making it a widely used method for motor speed control in various applications.
What is the role of feedback systems in DC motor controllers?
Feedback systems, such as encoders, serve a crucial role in DC motor controllers by providing real-time information about the motor's speed and position. This data is then used by the controller to make instantaneous adjustments, ensuring precise control over the motor's performance. Feedback systems enhance accuracy and responsiveness, making them essential in applications where precision is critical, such as robotics and industrial automation.
Can a DC motor controller be used for different motor types?
DC motor controllers are primarily designed for DC motors, and their compatibility with different DC motor types may vary. While some controllers may work with various DC motor configurations, it's essential to verify compatibility with the specific motor specifications. Factors like brushed or brushless design, voltage requirements, and power ratings should be considered to ensure proper operation
Can I control multiple DC motors with a single controller?
The capability to control multiple DC motors with a single controller depends on the specifications of the controller itself. Some controllers are designed to support multiple motor control, while others may be intended for use with a single motor. Examining the documentation provided with the controller is crucial to determine its capacity and limitations regarding the number of motors it can effectively control.